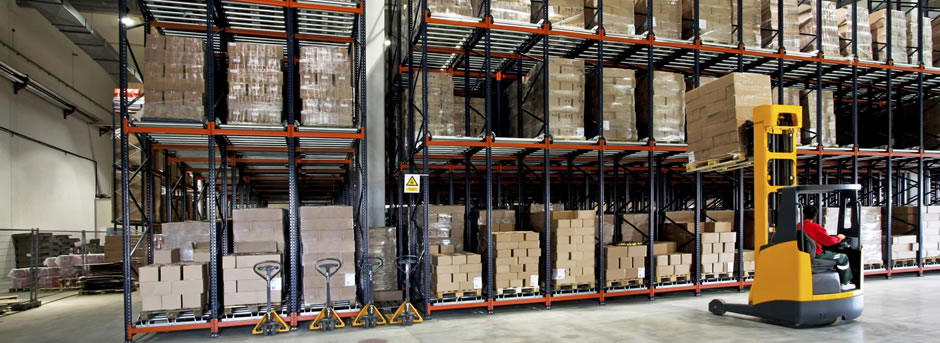
The Challenge:
The client, a manufacturer of medical equipment, launched a new production facility and struggled to control inventory. They operated out of two separate facilities, moved from the old to the new facility over time. During the transition, they implemented a new WMS and the combination of the physical migration and data migration caused them to lose control of the inventory on-hand. In addition, the new system had functionality that was not configured correctly, there was a lack of operator training, and no controls were in place to reveal the problems. The impact of this was several millions of dollars in write-offs and massive labor waste in trying to find material and conducting inventory audits.
Results:
We executed a plan to reconcile the inventory prior to a physical inventory with the help of the inventory control team, cycle counting 20,000 locations. We then created Standard Operating Procedures and visual management tools to mitigate sources of inventory issues. We helped build analytics out of their data warehouse that would provide daily metrics for inventory adjustments, to be able to monitor and control going forward.
Highlights this client achieved include:
- Inventory accuracy improved by 25%
- Cycle count accuracy improved by 30%